Quand la 3D permet de réduire le temps de maintenance
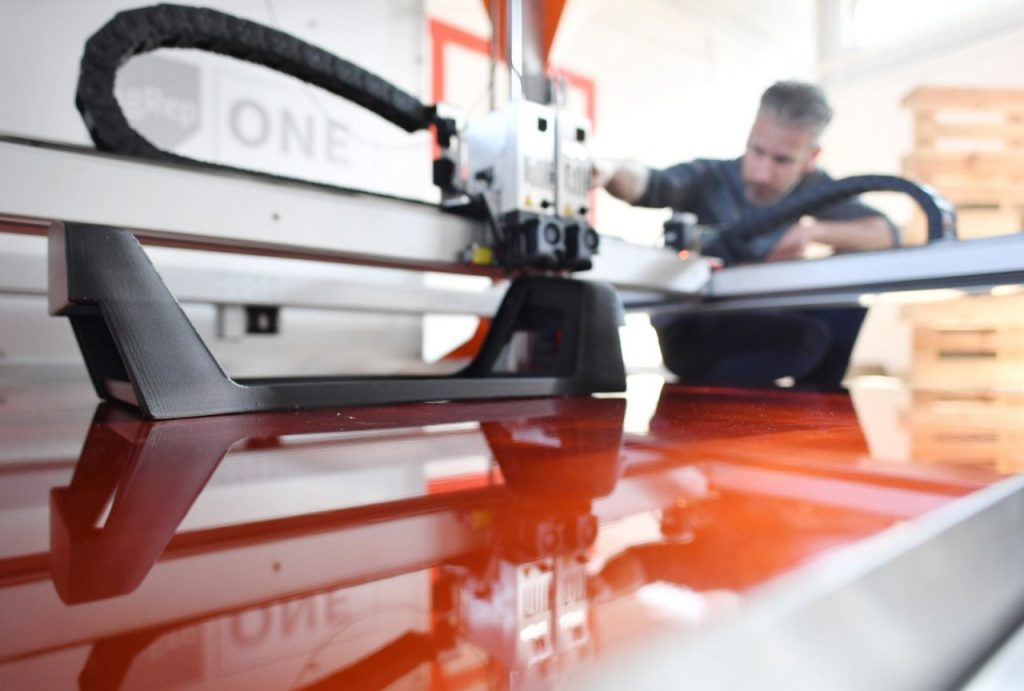
Les progrès sensibles en matière de création 3D permet de fabriquer des pièces rapidement sans devoir les commander ni les stocker.
C’est une évidence : actuellement, pour fournir une fiabilité maximale au service des trains, des quantités de commande minimales de pièces de rechange sont souvent requises. Elles sont d’ailleurs souvent incluses dans le contrat de commande et encombrent les allées de stockage de certains grands dépôts.
Il en résulte dès lors un stock de pièces de rechange ainsi que des outils qui ne sont pas toujours nécessaires au quotidien. Tout cela a un coût, dès l’instant où la plupart des entreprises ferroviaires sont des entreprises étatiques.
Bien des années après leur mise en service, les pièces de rechange sont souvent difficiles à obtenir pour le matériel roulant. Comme d’autres opérateurs en Europe, la Deutsche Bahn mise à l’avenir sur l’impression 3D pour les pièces de rechange de ses trains. Les temps d’immobilisation du matériel roulant peuvent ainsi être réduits.
Daniela Gerd tom Markotten, directrice de la numérisation et de la technique à la DB, explique le défi : « Nos trains doivent rouler pour nos clients et ne pas rester à l’atelier. L’impression 3D nous permet de nous procurer plus rapidement des pièces de rechange et de reconstruire nous-mêmes les pièces qui ne sont plus disponibles. Je suis fier de voir le nombre d’idées que nos collaborateurs ont développées et continuent de développer pour l’utilisation de l’impression 3D ».
Rapidité et sur mesure
Grâce au procédé d’impression 3D, la DB peut imprimer en peu de temps des pièces de rechange qui, sinon, seraient liées à de longs délais de livraison ou ne seraient plus du tout disponibles.
À Neumünster, dans le Schleswig-Holstein (nord), la Deutsche Bahn a investit environ 350.000 euros dans la technique. Pour l’ensemble du groupe, cela représente jusqu’à présent environ 750.000 euros. Selon la direction des lieux, d’ici 2030, environ 10 000 composants devraient pouvoir être fabriqués par impression 3D, ce qui correspondrait à environ un dixième des pièces utilisées dans l’entretien des véhicules.
Dans son atelier de Nuremberg, couche après couche, une tête d’impression se déplace de gauche à droite. La buse dépose le matériau avec précision. Ce qui, au début, ressemble encore à un simple rectangle bidimensionnel prend lentement forme. Après quelques heures, le résultat est là : l’imprimante 3D a fabriqué un nouvel appui-tête pour un siège de l’ICE.
Ce n’est qu’une des 100 pièces différentes que la DB fabrique déjà aujourd’hui par impression 3D, parmi lesquelles des roues de ventilateur, des appuie-tête pour trains régionaux, des boîtiers les plus divers, ou encore de petites pièces à grand effet : des pièces de rechange pour machines à café et les crochets de manteau pour les trains ICE.
Des résultats prometteurs
Tous les composants issus de l’impression 3D sont soumis à des tests approfondis avant d’être utilisés, par exemple des tests de résistance à la fatigue. La fabrication additive, c’est-à-dire la construction par couches, permet en outre d’optimiser au préalable les pièces de rechange aux endroits particulièrement sensibles aux pannes.
Cela permet de minimiser l’usure en amont et d’augmenter encore la disponibilité des trains. Alors que les premières pièces imprimées étaient exclusivement en plastique, le plus souvent en polyamide, des pièces métalliques sont désormais également produites par le procédé d’impression par poudre.
L’impression 3D permet de contourner d’éventuels goulots d’étranglement dans la livraison et économise des coûts. En plus de ses propres pièces de rechange imprimées en 3D, la compagnie ferroviaire coopère avec des entreprises et achète par exemple des pièces métalliques imprimées en 3D.
En outre, l’utilisation de cette technique est plus rapide, moins gourmande en ressources et parfois moins chère que les achats par des moyens conventionnels.
Depuis 2015, la Deutsche Bahn a utilisé plus de 30.000 pièces issues de l’impression 3D pour 500 applications différentes. D’abord légères et petites, l’impression 3D permettrait aujourd’hui à la DB de construire des pièces pesant jusqu’à 27 kilos pour ses ICE.
Articles similaires :